于是,一個多世紀以來,科學家和工程師們建立和測試了數學模型并考慮到刀具所受到的力,以估算預期的刀具壽命。很多這樣的模型都重點關注特定刀具在某些材料和加工中的性能,并通過簡單的公式和重復性測試獲得有效的刀具磨損情況預測。但可以應用于多種工件材料和刀具的廣義模型更適合工業應用。這些模型考慮到了多種刀具磨損因素,因此它們的數學復雜性也隨著所考慮因素的數量而相應增大 - 因素越多,計算越復雜。
盡管通過手寫數學公式和手工計算即可對簡單的刀具壽命等式進行求解,但仍然需要在生產環境中花費適量的時間,利用當今的計算機分析來對復雜模型的等式進行求解。數字計算非??煽?,但制造商應當對結果保持批判態度,尤其是在加工高級工件材料和使用極端加工參數時。整體而言,刀具壽命模型的發展過程將學術理論和實際應用緊密結合在了一起。
Archard 模型
對磨損過程進行的建模不僅僅局限在金屬切削應用領域。在 20 世紀 50 年代,英國工程師 John F. Archard 開發出了一個經驗模型,用于根據表面粗糙度的變化來計算滑動表面的磨蝕性磨損速度。他的等式是:
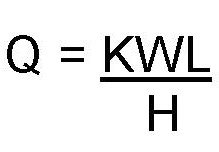
但 Archard 模型并未說明刀具磨損現象,而是預測了隨時間變化的磨損漸變速度。此模型涉及到兩個表面互相干擾的速度、機械負載、表面強度、材料屬性和磨損系數的影響。
但應當指出,Archard 模型不是專門為金屬加工領域常見的高速應用而開發的,它也并未涉及到溫度對磨損過程的影響。在金屬切削所產生的 900?C 高溫條件下,表面強度和磨損系數都會發生變化。這樣,Archard 模型本身就無法充分說明金屬切削領域的刀具壽命。
Taylor 模型
在 20 世紀初期,美國工程師 F.W. Taylor 開發出了一個刀具壽命模型,此模型包含了與金屬切削相關的因素。Taylor 發現,增大切削深度只對刀具壽命產生極小的影響,增大進給量所產生的影響稍大一些,而提高切削速度對刀具壽命產生的影響最大。下圖顯示了提高速度(藍色的 vC)、增大進給量(灰色的 f)和增大切削深度(黑色的 ap)之后所產生的刀具磨損。
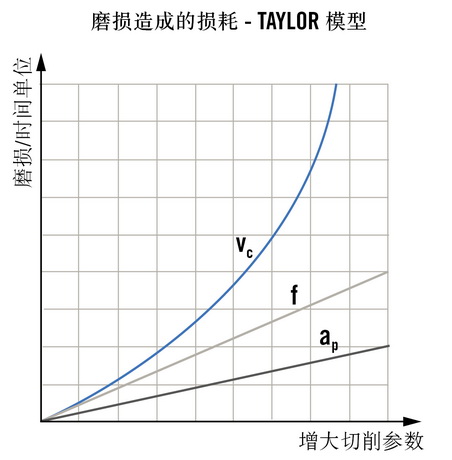
Taylor 還發現,刀具通常在開始運行時加速磨損,并在第二階段趨于穩定但慢慢增大,最終進入快速磨損的第三階段(也就是最終階段),直到刀具壽命結束。他設計的模型展示了第二階段與第三階段之間的時間長度。
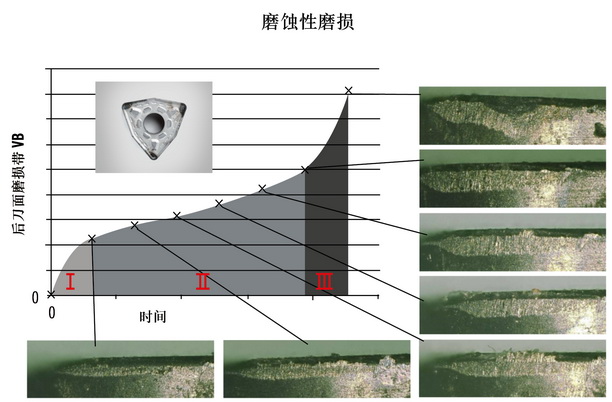
最初的 Taylor 模型關注切削速度的影響,在切削深度和進給量保持不變的情況下有效。確定了切削深度和進給量之后,可以控制速度以改變刀具壽命。
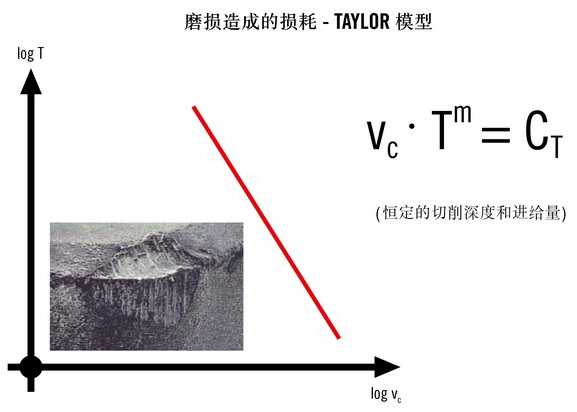
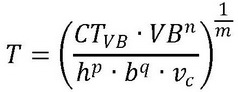
最初的 Taylor 模型也無法充分說明切削刀具與工件之間的幾何關系。可以讓切削刃從直角方向(垂直于進給方向)或斜向(以相對于進給方向的前角)切削工件。此外,當切削刃的拐角不參與切削時,切削刃將被視為“自由”切削,當刀具的拐角參與工件的切削時,切削刃被視為“非自由”切削?,F代金屬切削應用中很少涉及自由直角切削或自由斜向切削,因此它們很少被提及。Taylor 的擴展等式增加了一個切削刃前角變量,但不允許刀具的拐角參與切削。

切屑厚度的角色
隨著工程師們對刀具壽命模型不斷進行開發和研究,一個事實變得明顯起來,那就是所產生的切屑厚度與刀具壽命密切相關。切屑厚度是在垂直于切削刃的方向和垂直于切削方向的平面中測量出的切削深度和進給量之間的一個函數。如果切削刃的角度是 90?(在美國是 0? 主偏角),則切削深度和切屑寬度相同,
進給量和切屑厚度也相同。
刀具拐角參與工件切削的程度增加了另一個用于確定切屑厚度的變量。瑞典工程師 Ragnar Woxén 于 20 世紀 60 年代開發出了一種用于說明刀具刀尖圓弧吃刀程度的方法。他提出了一個用于計算車削加工中的等效切屑厚度的公式,該公式可計算出刀具刀尖的理論切屑厚度。這一成果非常透徹地分析了刀尖圓弧,并能夠利用矩形來說明切屑面積。借助這一描述,模型可以反映刀具圓形刀尖圓弧的吃刀程度。
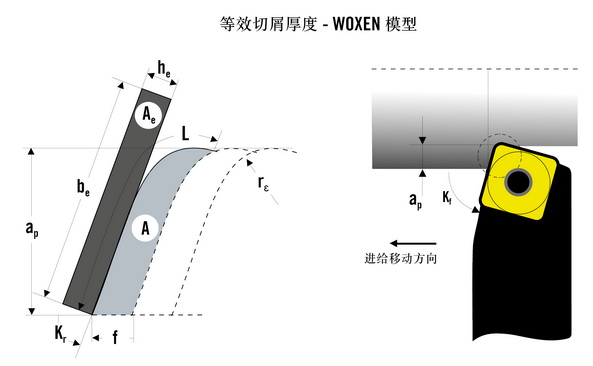
瑞典教授 Bertil Colding 于 20 世紀 50 年代開發的一個刀具壽命模型,此模型說明了刀具壽命、切削速度與等效切屑厚度之間的關系,并考慮到切削工藝中的其他因素。這些因素包括刀具材料和形狀、溫度以及工件可加工性。使用此模型和它復雜的等式可以準確地計算多種切削條件同時變化時所產生的后果。
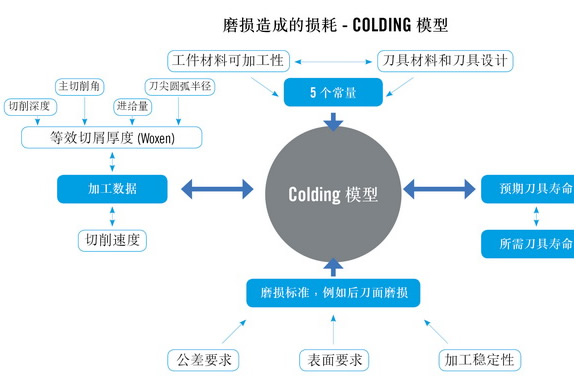
另一方面,如果減小等效切屑厚度,刀具壽命將會延長,提高刀具速度后所產生的影響也會下降。進給量、切削深度、主偏角和刀尖圓弧的很多組合都可以取得相同的等效切屑厚度值。如果在恒定的切削速度下保持恒定的等效切屑厚度,則無論切削深度、進給量和主偏角如何變化,刀具壽命都將保持不變。
左圖顯示了在 Taylor 模型的穩定磨蝕性磨損條件下進行加工時,等效切屑厚度(由 he 表示)的變化
與刀具壽命 (T) 和切削速度 (vc) 之間的關系。右圖中也顯示了這一直線關系。但由于 Colding 模型考慮到了其他磨損因素,因此也用另外一條曲線顯示了此模型的預測結果。
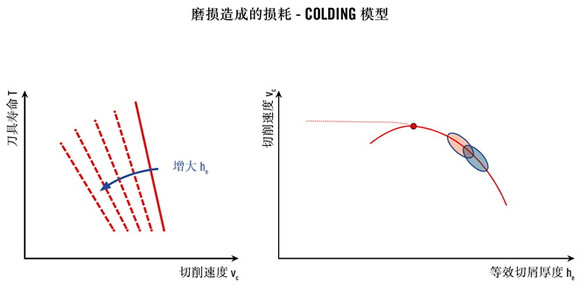
但該曲線表明,在局部的切削范圍內,更大切屑厚度與更高切削速度的組合或者更高生產率的切削條件可以延長刀具壽命。20 世紀 60 年代和 70 年代誕生了同時增大兩種切削參數和提高金屬切除率這一概念,這一突破性理念與當時的經驗和直覺恰好相反。
通過開發包含金屬切削工藝多種因素的模型(例如 Colding 模型)以及 Taylor 和 Archard 模型的概念,將理論和實際緊密結合在了一起。
實際應用日益復雜的刀具壽命模型時,需要對它們采用的多種因素執行計算機分析。在短時間內,可以手動計算出專門用于特定刀具、工件材料和切削條件的簡單模型的結果。在某些情況下(例如手工計算時),基本 Taylor 模型可以在相對較短的時間內得出結果。
但即使是擴展的 Taylor 模型也可能需要大量的手工計算時間,因此在生產環境中對 Colding 等式中的因素進行手工計算是不切實際的。為了充分利用這些高級模型的預測能力,制造商們應使用計算機的計算程序(請參閱關于山高的 Suggest 的附注)。這些程序可以在幾秒鐘甚至更短的時間內對復雜等式進行求解并提供有用的加工指導。不過,電子計算輔助工具依然要求機械師以審慎的態度進行思考,并將結果與自己在車間實際工作中獲得的常識和經驗進行比較。
結論
最后,刀具壽命建模并不是一種純學術追求;它可以幫助制造商提高生產率和控制成本。制造業重點考慮的是需要花費多少時間和成本才能生產出特定數量的合格工件。了解在需要更換刀具之前刀具能夠準確、高效地切削多長時間非常重要。工藝可靠性以及對刀具成本和停機時間進行的控制取決于是否能夠準確地預測刀具壽命。模型還允許更改工藝以便最大限度提高速度、質量或可靠性。切削刀具壽命模型的進一步發展能夠幫助制造商精密調整自己的工藝并實現自己的生產目標。
附注 計算機輔助計算
在生產環境中,所有的機床操作員都希望知道切削刀具在出現磨損或失效之前還能堅持多久。但與此同時,他們還必須在刀具使用壽命內充分地應用刀具。刀具壽命建模已經從簡單地手工記錄個別運算的結果發展為運用復雜的模型并以數學方式納入盡可能多的切削工藝變量。
少數幾個能夠快速完成的手工計算方式基本上能夠得出有價值的刀具壽命估算值。模型越復雜,所需的計算和時間就越多。最好的模型能夠提供與現實緊密契合的刀具壽命預測。但如果在實施復雜模型時進行計算所花費的時間不少于加工本身所花費的時間,它的經濟效益就值得商榷了。因此,可以使用計算機的計算程序,它們能夠快速和絕對準確地處理高級切削刀具壽命模型所涉及到的因素。
其中一個示例是山高提供的 Suggest 在線資源。作為山高 My Pages 數字站點中的一個 Portlet,Suggest 是一款免費的應用程序,適用于 iOS® 或 Android® 平臺的移動設備和具有網絡瀏覽器的計算機。
Suggest 利用山高 80 多年來積累的金屬加工經驗為新的作業提供切削刀具建議或為重復性項目提供刀具選擇方案。這款應用程序匯集了數千種切削刀具產品和應用程序的綜合數據,可以根據用戶的輸入提供完整的刀具建議。
Suggest 不僅僅是一個在線目錄,它還是一款先進的產品選擇器,可以快速找到用于在要求公差范圍內加工零件的刀具和一系列工序。Suggest 可以根據極少的數據提供建議。不過,用戶輸入的信息越多,所提供的建議就越貼切。每個數據輸入字段中的默認值讓具有各種金屬加工技能水平的用戶都能夠得心應手。用戶可以隨時調整自己輸入的數據,并過濾、排序和比較信息以便精密調整建議。所有刀具建議都可以保存下來并以電子方式共享或者打印,以便于分發。
全面的資源有助于制定工藝規劃,而且便于為特定的作業找到高效且經濟實惠的刀具和切削策略。應用成熟的技術能力和和工藝規劃技能,可以大大縮短整體的工藝規劃時間。
作者:Patrick de Vos