摘要:砂輪輪轂的設計和制備材料決定了砂輪的動態、靜態特性;這些砂輪特性反過來又影響著砂輪的磨削性能。在砂輪受超大離心力和磨削力影響的高效深磨削(EHDG)工藝中,這些特性尤為典型。另一方面,通過進程中即時檢測和后處理測量的辦法對砂輪的動態特性進行控制是優化磨削工藝較為適宜的一種策略。本文利用兩種不同輪轂材料的CBN陶瓷結合劑砂輪進行實驗并對結果進行對比,從而研究碳纖維增強復合材料(CFRP)輪轂基體對磨削工藝的影響。實驗結果表明砂輪動態性能影響著材料去除機制并影響工件的表面粗糙度。此外,采用CFRP作為輪轂材料可以降低砂輪在加工過程中的徑向膨脹和磨削力。使用鋼材砂輪時的振幅和頻率較高,而使用CFRP輪轂材料的砂輪則可以使振幅和頻率衰減。
關鍵詞:CFRP,HEDG,進程中檢測,砂輪輪轂,動力特性
1、引言
HEDG工藝和緩進給磨削工藝只有在配置高性能磨床和配套砂輪以及適當潤滑劑的條件下才能實現高效磨削。在HEDG工藝中砂輪上的負載力較大且離心力相當大,因此砂輪的動力特性在整個工藝中就尤為重要。此外,HEDG工藝中由于砂輪和工件的速度較高,砂輪會產生彈性形變;受接觸剛度影響的彈性形變進而會影響材料去除機制并導致加工誤差。砂輪的接觸剛度定義為接觸區上施以砂輪法向壓縮力Fn和砂輪彈性形變δ之間的關系。接觸剛度受磨削參數、砂輪規格等的影響。
砂輪的另一個顯著特性是阻尼特性,該特性影響砂輪和工件在接觸區的振動并影響工件表面粗糙度和波紋度。另一方面,系統的不穩定性會在切割深度上發生規則振動,從而使得磨削力在砂輪上引起不規則磨損。
HEDG工藝通常采用CBN或金剛石超硬磨料。超硬磨料砂輪有涂附了一層超硬磨料的輪轂基體構成。輪轂基體的設計和材料影響著砂輪的靜態、動態特性。近年來,多種材料被用來制備超硬磨料砂輪的輪轂基體。輪轂基體材料的基本要求有:熱傳導系數高、機械強度高、振動阻尼性能好。常見材料主要有:鋁、鋼材、金屬/非金屬填料的人造樹脂、陶瓷和聚合物等。
輪轂材料的選擇取決于砂輪的加工區。高速高性能深磨削工藝則采用鋼材和鋁材等強度高的輪轂基體。采用無心輪轂基體并對其橫截面施以恒定應力可以實現500m/s的圓周速度。本實驗實際最大圓周速度為280m/s。由于鋼材和鋁材的彈性模量-密度比作為材料化學組份函數關系的差異很小,所以在給定旋轉速度的條件下,張力基本都相同。
制備高性能砂輪的另一種材料是碳纖維增強復合材料(CFRP),CFRP材料的強度和剛度極高,強重比極大。實現鋼材輪轂到CFRP輪轂的材料升級可以降低砂輪膨脹3倍。碳纖維(CF)含量較低的CFRP輪轂可用于砂輪低速加工,具有輕量的優勢。由于密度低,材料重量可減輕90%左右,CFRP可以提供額外的阻尼。
輪轂材料特別是CFRP特性對磨削工藝的影響鮮有研究。Muckli利用有限元素法在305m/s的較高切削速度條件下研究鋁材和鋼材輪轂制備而成的砂輪性能。研究表明輪轂基體的幾何形狀和材料都會影響砂輪上陶瓷結合劑CBN層上的應力。研究還發現鋼材輪轂基體容易出現輕微膨脹,但應力較高。
Warnecke等人對比了人造樹脂-鋁材復合物輪轂和硬性鋁材輪轂的性能。結果表明軟性人造樹脂-鋁材輪轂發生了顯著形變,而硬性鋁材輪轂則穩定。此外,磨削力和材料去除機制受砂輪輪轂彈性和切削速度的影響。
本研究采用CFRP和鋼材作為CBN砂輪的輪轂材料,用于淬硬鋼工件的高效深磨削加工,以此來研究CFRP輪轂材料是如何影響磨削工藝的。研究結果主要側重于砂輪振動和形變,磨削力和磨削表面質量。
2、實驗裝置
2.1 測量系統
為研究分析輪轂材料對磨削工藝的影響,需要對加工過程中輪轂基體上的振動傳播進行探測記錄。
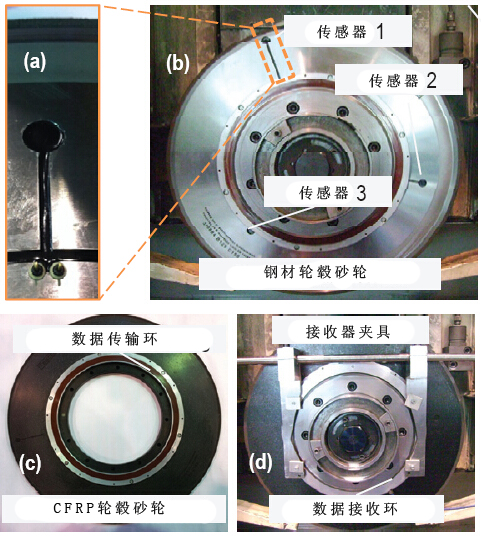
2.2 實驗參數
表1為實驗參數。表2為砂輪輪轂材料的機械性能。實驗所用機床和相關設備如下:
機床工具:Elb 微切削AC8 CNC通用平面磨床;
表面粗糙度和輪廓儀:Hommel-Werke型T-8000;
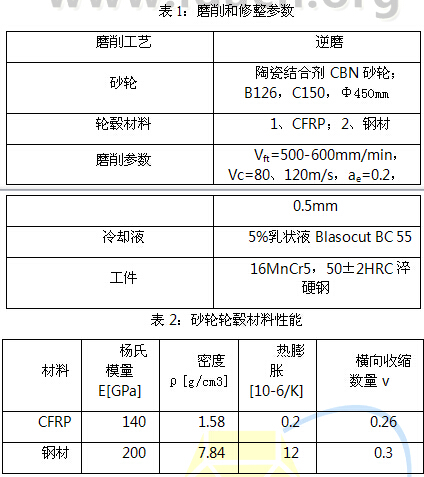
在HEDG工藝和緩進給磨削工藝中,切割深度會產生相當大的砂輪負載。這種現象主要發生在碎屑不能隨冷卻液完全清除掉時。在砂輪表面采用高壓清理噴射可以防止砂輪發生負載,流速建議設置為0.3 lit/分鐘,壓力80 bar。這些措施主要取決于液體壓力而非體積流量。它可以影響砂輪的動力特性。
鑒于此,在類似條件下對使用高壓清理噴嘴的兩種砂輪的動力特性進行該研究。實驗結果表明高壓清理噴嘴能夠引起撒花輪振動,如圖2所示。圖中使用和未使用清理噴嘴得出的CFRP信號對比就證明了這一點。鋼材輪轂砂輪的振幅明顯比CFRP輪轂砂輪的振幅要大,利用CFRP輪轂材料就可以衰減砂輪的振動。
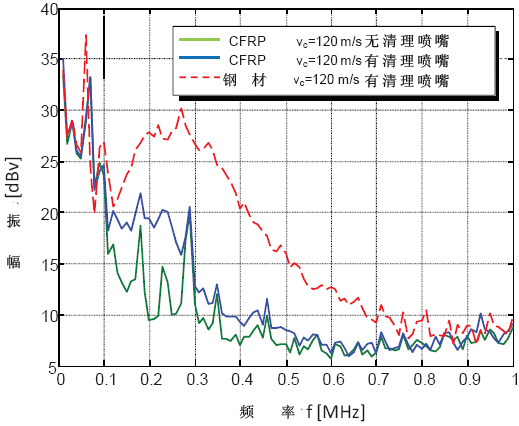
據圖可知,CFRP較高的阻尼可以顯著降低輪轂振幅;而寬頻帶鋼材砂輪的振幅譜主要是由鋼材較低的阻尼所致。
輪轂材料還影響砂輪的接觸剛度以及離心力導致的砂輪徑向膨脹。因此,砂輪接觸區的集合形狀會受到輪轂材料的影響;而通過以下試驗則可以得到改善。首先,以恒定切割深度0.1mm、切割速度15m/s和進給速度50mm/min研磨出4個槽。選取槽1和槽4作為外槽基準,以此測量其他槽的深度。第二個槽以切割深度0.5mm、切割速度120m/s、進給速度500mm/min僅研磨一個周期。第三個槽按照第二個槽的參數來加工。然后在沒有其他額外橫向進給條件下對其研磨10個周期。第三個槽的深度可用來檢測砂輪膨脹,第二個槽的深度用來計算砂輪的接觸剛度。
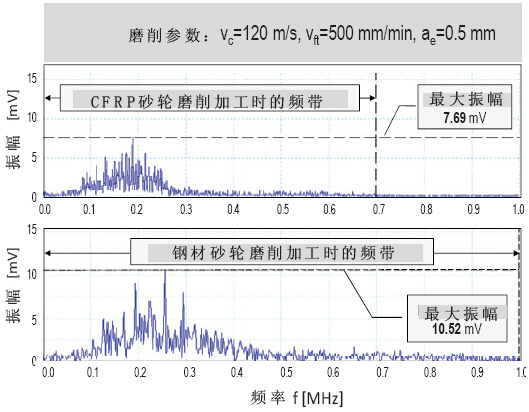