采用傳統的機械研磨方法制造金剛石刀具時,因研磨線速度高,局部壓力大,對刀具表面及刃口沖擊劇烈,不可避免地會導致刀具表面產生微小溝紋和較厚的加工變質層,且刀刃鋸齒度較大,從而限制了刀具質量的進一步進步。試驗表明,采用機械方法研磨金剛石的表面粗糙度極限值約為3nm,刀刃鋸齒度最小只能達到幾十納米的數目級,表面加工變質層厚度約為200nm。
隨著超精密加工技術的不斷發展以及加工精度的不斷進步,對金剛石刀具的精度及質量要求也更為苛刻。研究還發現,刀具表面變質層厚度將直接影響刀具的壽命與零件的加工質量。因此,開發新型的金剛石刀具加工方法無疑是突破機械研磨方法對刀具質量限制的有效途徑。
此外,如高精度輪廓儀、隧道掃描顯微鏡、原子力顯微鏡等儀器中使用的金剛石探針的前端球頂圓弧半徑要求達到或小于1~2μm,精度要求高于0.1μm;加工光通訊用光柵表面的微細溝紋時,需要使用刀尖圓弧半徑為0.1~3μm,并具有相當高的尺寸與外形精度的金剛石雕刻刀具。對于此類特殊要求,采用傳統的機械研磨方法或者無法達到,或者加工本錢極高,因此也迫切需要開發新型的金剛石工具加工方法。
下面介紹近年來出現的四種較為典型的金剛石工具加工方法。
2 離子束濺蝕法
離子束濺蝕法是利用高能離子的轟擊作用直接對被加工工件進行物理濺蝕,以實現原子級的微細加工。離子束濺蝕法的加工原理如圖1所示。
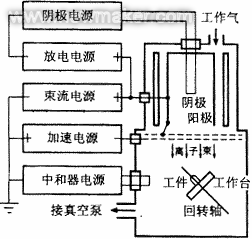
3 真空等離子化學拋光法
真空等離子化學拋光法的加工原理如圖2所示。轉動的磨盤被中間的高真空區分為左右兩部分。左邊為沉積區,采用真空等離子物理氣相沉積法在磨盤表面鍍上一層細晶粒氧化硅;右邊為研磨區,金剛石表面處于活化狀態的碳原子通過與磨盤上的氧化硅發生分子級化學反應而形成磨削作用。反應天生的一氧化碳或二氧化碳氣體被真空泵抽出反應室。該方法的研磨速度為1~3000μm3/s,約每秒0.25~750個原子層,可研磨出極高質量的刃口。該方法最先被美國刀刃技術公司用于研磨超精密金剛石鏡面切削刀具,該刀具可廣泛用于加工各種納米級精度的超精表面。
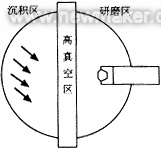
圖2真空等離子化學拋光法的加工原理
4 無損傷機械化學拋光法
該方法是在NaOH溶液中加進適量的細金剛石粉和更細微(達納米級)的硅粉,帶強負靜電的細微硅粉會吸附在粒度大得多的單個金剛石微粒上形成具有硅吸附層的金剛石磨料,然后將其涂敷在多孔的鑄鐵磨盤上對被加工金剛石進行研磨。研磨時,吸附在金剛石微粒上的硅粉一方面可阻止金剛石微粒對被加工金剛石表面的直接沖擊,保護金剛石表面不會產生深度損傷,另一方面可與被加工金剛石表面發生反應并通過其微弱的磨削作用將反應層往除。該方法的磨削速度非常低,僅為每分鐘一個原子層。
5 熱化學拋光法
在溫度為800℃時,若使金剛石表面與鐵接觸,金剛石晶體中的碳原子能夠擺脫自身晶格的約束,擴散到鐵晶體晶格中往。熱化學拋光法即是運用此機理對金剛石表面進行研磨加工。
研磨時,在氫氣氣氛中將鐵質研磨盤加熱到800℃,使被加工金剛石表面與鐵質研磨盤接觸并相對滑動,金剛石晶格中的碳原子就會擴散到鐵晶體晶格中,達到磨削金剛石的目的。進進鐵晶格中的碳又與氫氣反應天生甲烷并隨氣流散發到空氣中。該方法的磨削速度為每秒40~2000個原子層。
利用該方法刻蝕金剛石,還可在其表面加工出圖案和花紋,制成各種精美的金剛石工藝品。
6 結語
上述加工方法具有以下共同特點:
對被加工金剛石表面無沖擊,避免了機械加工方法造成的表面沖擊溝痕,使被加工表面異常光潔,其表面粗糙度可達1nm。
被加工金剛石表面與研磨盤之間的接觸力非常小,易于研磨出高質量的刀刃。
被加工金剛石表面的損傷與變質層較磨削速度很低,只適用于精磨加工后的超精密拋光。
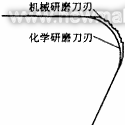
圖3機械研磨與化學研磨的刀刃圓弧比較淺,可進步金剛石刀具的壽命。
此外,采用機械方法加工制成的金剛石刀具用于鏡面切削時,通常存在一個“磨合期”,即需要經過一段時間的切削過程,刀具才能達到最佳加工效果。究其原因,是由于刀刃圓弧實際是由一些不規則的折線組成。研究文獻表明,化學研磨方法可得到比機械加工方法光滑得多的刀具刃口圓弧(如圖3所示),制成的刀具在使用過程中可消除“磨合期”,且工件表面加工質量得以大幅度進步。