微型零部件由于占用空間少、耗材少、能耗低而廣泛應用于工業領域,微型加工工藝便應運而生,微銑削工藝便是其中之一。微加工銑削,也叫做微銑削,是硬質材料模具制造中常用的工藝。微銑削在航天航空、汽車、生物制藥、電子、信息技術、電信等應用到微型零部件的領域都有所涉獵。隨著諸多設備微型零部件的生產和微型化復雜性的增加,加工材料也由傳統的軟材料(鋁,銅等)轉為硬質工程材料,如超合金。但超合金的熱導率低,硬度高,對這些材料進行微加工存在一定難度。
Ti-6Al-4V是一種含有6%鋁和4%釩的鈦合金,具有良好的承重性和抗腐蝕性、質材輕、極限抗拉強度高、熱導率和電導率低;熔點高、熱穩定性好。常用于飛機結構部件、飛機機身、渦輪葉片、熱交換器零部件和賽車零件等。鑒于Ti-6Al-4V合金的以上性能,對其進行微型零部件加工就不能用傳統的工藝如澆鑄、成型等;而是采用放電微加工,微銑削等加工工藝。放電微加工工藝由于耗時長,微銑削便成為最佳加工方法。
本研究就表面粗糙度和毛刺寬度對重要的切削參數如工具類型、主軸轉速、軸向切削深度和每齒進給量進行分析;并通過多目標優化的方法得到切削參數的優化值,最終減小表面粗糙度和毛刺寬度。
實驗
本研究由實驗和工藝優化兩部分組成。通過實驗來研究切削參數對表面粗糙度和毛刺寬度的影響;石川圖用來分析影響表面粗糙度和毛刺寬度的因子;根據以前的文獻選擇重要的因子,并在本研究做了文獻綜述。微銑削過程中采用田口正交陣列L18進行工藝優化以找到最佳參數。
文獻綜述
Lai 通過尺寸效應、微型刀具的刃口半徑和最小切屑厚度進行建模并分析了微銑削加工工藝。首先用修改后的JC方程對微米級材料進行建模,然后建立微米正交切削FE模型,并在此基礎上建立OFHC Cu微銑削的切削力模型。研究結果表明當未切屑厚度小于最小切屑厚度時剪切力大大增加。
Aramcharoen利用TiN,CrN,TiCN,TiAlN 和CrTiAlN鍍附工具和未鍍附工具對脆硬鋼微銑削加工的影響得出結論:TiN鍍附在銑刀磨損和表面拋光方面能達到最佳加工效果。
Ozel 研究了CBN鍍附對Ti-6Al-4V合金微銑削的影響。結果表明在銑刀磨損和表面拋光方面CBN鍍附工具要比未鍍附工具加工性能更加優越;CBN鍍附工具的工具溫度要比未鍍附的WC/Co工具溫度低。但尺寸效應、最小切屑厚度不甚理想。
Thepsonthi 利用田口正交陣列L9對合金微銑削的加工參數進行優化。研究對每齒進給量、軸向切削深度和主軸轉速進行了優化,并建立了RSM模型。
Ding H根據實驗評價和數值模擬對淬硬鋼H13微銑削加工的表面粗糙度、尺寸效應和銑刀磨損進行了研究;用FE模型對微切槽和微側銑加工過程中的切屑形成進行了模擬。
實驗
實驗采用有效切削直徑為500μm的TiN鍍附和未鍍附工具在微加工中心上進行Ti-6Al-4V合金的微銑削。在表面粗糙度和毛刺寬度方面對工具鍍附、主軸轉速、軸向切削深度和每齒進給量等參數進行了研究。每次實驗都求得表面粗糙度(Ra)和毛刺寬度的平均值。用Mitutoyo SJ-301數字表面光潔度檢查儀在切槽底部進行表面粗糙度測量;在切槽兩邊沿形成的毛刺的寬度即毛刺總寬度,由光學顯微鏡測得。圖一為實驗裝置。圖二為石川圖,分析了諸多因素對表面粗糙度和毛刺寬度的影響。
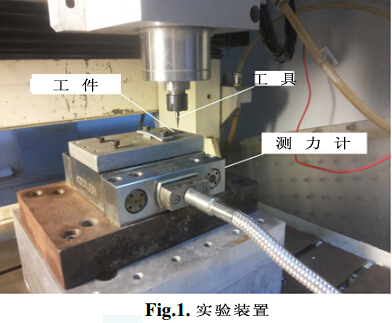
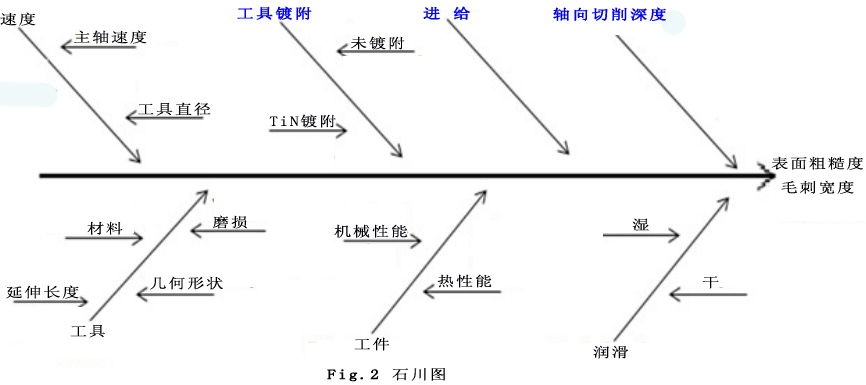
鍍附類型、主軸速度、每齒進給量、切削深度。
表一為這些加工參數的值。其中,工具類型有兩個量級因素,切削速度、進給速度和切削深度有三個量級因素。實驗設計采用正交陣列L18,它可以擁有一個控制因子,兩個量級;總共多達七個因子,每個因子三個量級。18組實驗即可有效計算出主要效果。
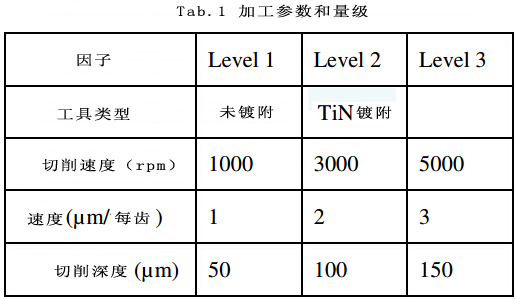
切削參數對毛刺寬度影響
圖三為微銑削過程中光學顯微鏡(變焦 ×50)下觀察到的毛刺形成頂視圖。逆銑的毛刺要比順銑的毛刺多;將逆銑和順銑毛刺寬度相加從而得出毛刺總寬度。圖四、五、六和七分別為工具類型、主軸速度、每齒進給量和軸向切削深度變量。
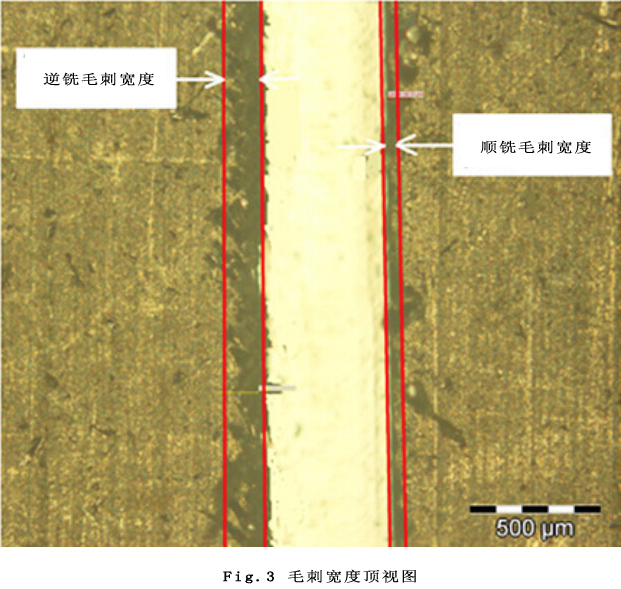
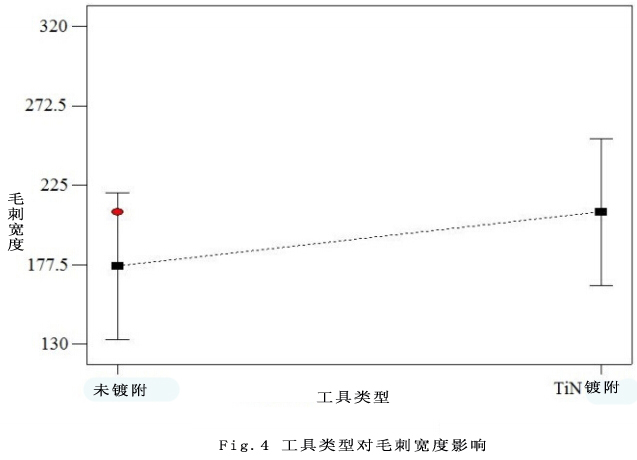
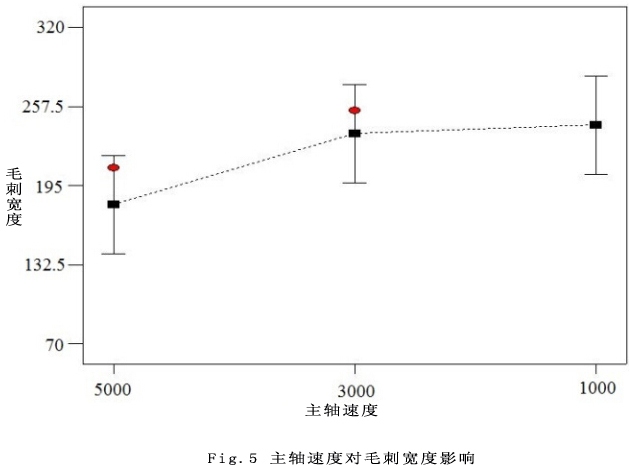
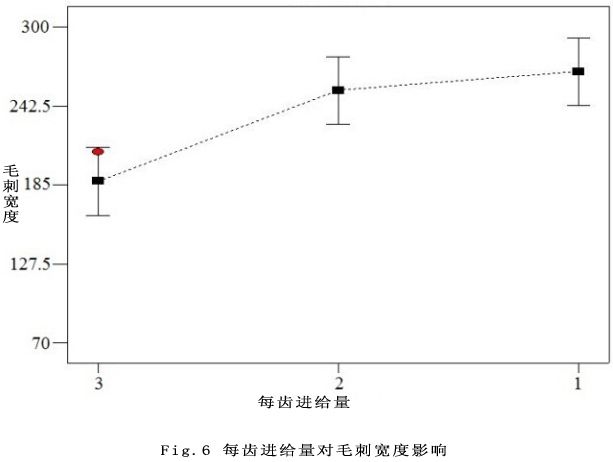
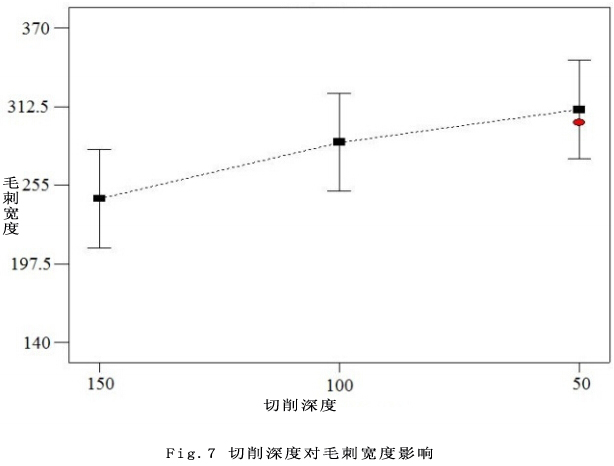
圖四可以明顯看出TiN鍍附工具比未鍍附工具產生的毛刺更多,這可以是鍍附了TiN的工具的切削刃半徑較大的緣故。圖五、六可以看出毛刺寬度隨著每齒進給量和主軸速度的增加而變小;毛刺寬度還隨軸向切削深度的增加而減小。從這些圖標可以看出,軸向切削深度對毛刺寬度影響最大。
切削參數對表面粗糙度影響
圖8、9、10、11分別為工具類型、主軸速度、每齒進給量和軸向切削深度變量。表面粗糙度隨切削參數和工具類型的變化如圖8所示。TiN鍍附工具的微銑削比未鍍附工具的微銑削加工能夠產生更好的表面光潔。這是由于工具鍍附增加了刀尖半徑。
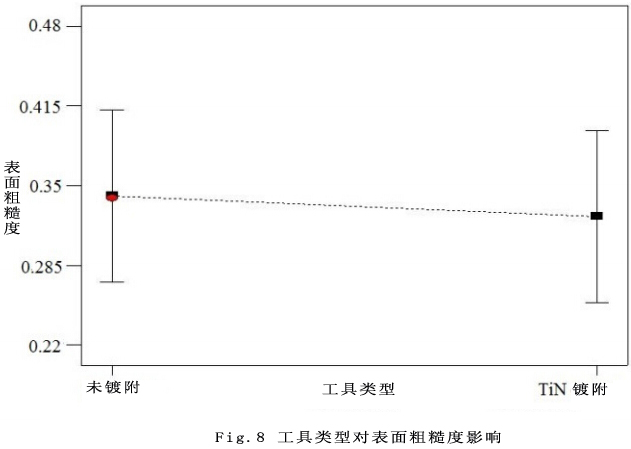
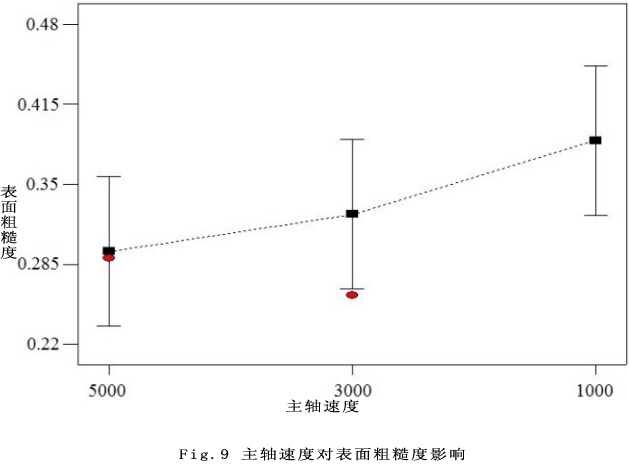
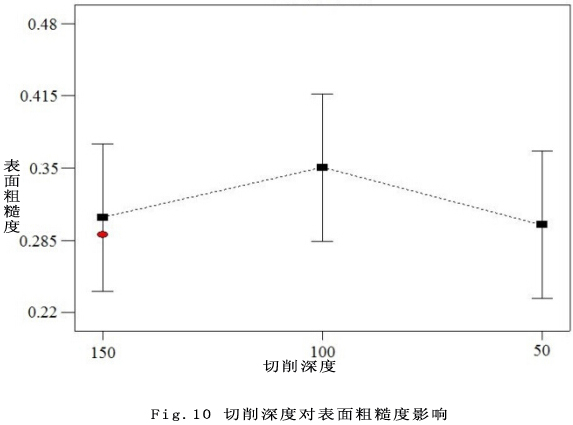
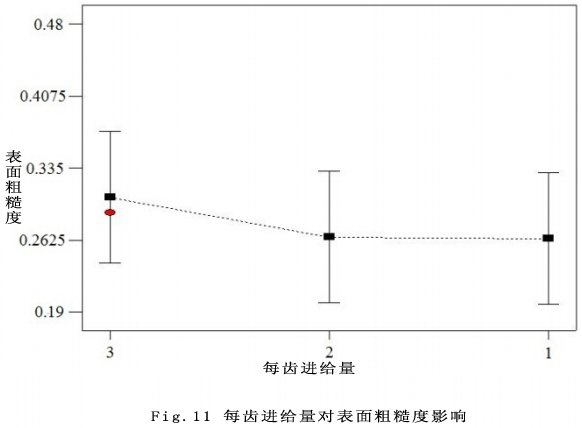
從圖中還可以看出表面粗糙度隨著主軸速度的增加和進給速度的降低而有所改善。速度增大時產生更多熱量從而軟化工件,這可能就是切削速度較高時表面粗糙度較好的原因。隨著每齒進給量的增加,表面粗糙度也會有所增加。
結論
本實驗研究了切削參數對毛刺寬度和表面粗糙度的影響,并進行優化求得減小毛刺寬度和表面粗糙度的切削參數值。有以下結論:
•TiN鍍附工具要比未鍍附工具產生更多毛刺;隨著主軸速度、每齒進給量和軸向切削深度的增加,毛刺寬度變小。
•TiN鍍附工具要比未鍍附工具產生更好的表面光潔度。表面粗糙度隨著主軸速度的增加而降低、隨每齒進給量的增加而增大。
•毛刺總寬度優化值為88.33 μm,表面粗糙度值為0.2594 μm,該數值為TiN鍍附工具、每齒進給量為3 μm/齒、主軸速度為5000 rpm、軸向切削深度為50 μm的條件下求得。