摘要 碳纖維復合材料(CFRP)具有高強度、高剛性、良好的抗疲勞性和抗腐蝕性等優點,已廣泛應用于航空航天、國防軍工等高端裝備制造領域。飛機機翼、垂尾和尾錐等、火箭的排氣椎體、發動機和助推...
碳纖維復合材料(CFRP)具有高強度、高剛性、良好的抗疲勞性和抗腐蝕性等優點,已廣泛應用于航空航天、國防軍工等高端裝備制造領域。飛機機翼、垂尾和尾錐等、火箭的排氣椎體、發動機和助推器殼體等、人造衛星的承力結構、太陽能電池基板、復雜曲面天線和連接架等,宇宙飛船的翼面板和支撐構件等均采用碳纖維復合材料。碳纖維復合材料在軍用飛機上的使用量可達到50%,在民用大型客機上使用量可達到50%。復合材料用量已成為衡量航空航天產品先進性的標志之一。
民用飛機翼梁、桁條和蒙皮等結構件通常由各種不同成分的碳纖維復合材料構成。碳纖維復合材料結構件裝配時通常需要與作為承載支撐件(骨架或支架)的鈦合金和鋁合金零件局部連接,形成復合材料/合金(C/A,Composites/Alloy)疊層構件,C/A疊層構件主要采用鉚接和螺接的機械連接形式,裝配時需要加工大量連接孔。F-22戰斗機每副機翼上都有14000多個連接孔需要加工,一架波音747飛機則有300多萬個連接孔需要加工。CFRP和C/A疊層制孔成為飛機制造中極為重要的加工工序。
圖1 碳纖維復合材料制孔缺陷
連接孔的加工精度和質量是保證構件連接可靠性和壽命的關鍵。飛機碳纖維復合材料結構件制孔數量多、難度大、要求高、工作繁重,裝配制孔的精度和質量要求更高,對制孔技術提出了新的挑戰,亟需專用高性能制孔刀具和高效精密制孔工藝。
CFRP制孔的主要問題
飛機結構件碳纖維復合材料制孔存在的問題主要表現在以下幾個方面。
制孔精度和質量差,加工缺陷嚴重。如果采用傳統麻花鉆進行CFRP和C/A疊層制孔,鉆孔精度和表面質量差。特別是鉆孔時軸向切削力大,導致碳纖維復合材料產生纖維排列畸變、撕裂、層間分層和出口毛刺等缺陷,如圖1所示。鋁合金、鈦合金等由于屬于薄板制孔,也容易形成嚴重的出口毛刺。
制孔工藝流程長。由于缺乏合適的專用高性能刀具進行CFRP和C/A疊層制孔,為了保證C/A 疊層結構的制孔精度和質量,生產現場不得不采取“鉆孔-擴孔-粗鉸孔-精鉸孔-锪窩”多工序加工策略,造成工序和刀具多,成本高、工藝流程長、管理復雜,難以實現自動化。這是由于采用手持工具完成多工序加工時,制孔效率極低,制孔精度和質量的穩定性難以保證。
刀具磨損嚴重。由于碳纖維復合材料的硬度高和強度高等特點,導致刀具快速磨損,不僅影響加工精度和表面質量,而且使生產成本居高不下。
工藝參數匹配困難。C/A疊層制孔時,由于碳纖維復合材料與合金材料性質和可加工性差異很大,鉆削工藝參數的匹配和控制不當會導致嚴重的界面缺陷和出、入口缺陷。
制孔過程排屑不暢,熱影響嚴重。C/A 疊層結構制孔時,特別是CFRP/Ti合金疊層制孔時,鉆削合金會產生連續的高溫切屑,不僅不易排屑,而且高溫切屑排出時容易劃傷或燙傷復合材料內孔表面,影響制孔質量。
綜上所述,CFRP和C/A 疊層構件制孔與傳統金屬制孔具有巨大的區別,專用高性能制孔刀具和高效精密制孔工藝已成為航空航天領域復合材料構件裝配中的關鍵技術。
碳纖維復合材料制孔加工刀具性能要求
碳纖維復合材料制孔中應用的刀具結構類型較為復雜,主要包括麻花鉆(Twist drill)、匕首鉆(One shot drill reamer)、多面鉆(Multi-facet drill)、三尖鉆(Kevlar drill)、套料鉆(Core drill)等。通過鉆尖形貌和刀具角度的優化使得在鉆削碳纖維復合材料時碳纖維的切斷更輕快、順利,從而獲得更小的軸向力、更低的鉆削溫度、更高質量的孔是刀具匹配性能研究的主要目標。
在碳纖維復合材料加工中,大負前角的橫刃易引起過大的軸向力并可能造成分層。因此,通常采用X型或S型橫刃修磨方式來改變橫刃。匕首鉆嚴格來講是一種鉆、鉸復合刀具,由于有周向側刃作為主切削刃直接參與鉆孔,更易形成無毛刺、表面高質量的孔。匕首鉆在抑制毛刺生長方面的作用,在許多研究人員的試驗研究中得到了證實。多面鉆在碳纖維復合材料鉆削的應用,源于美國洛克希德公司通過成功采用八面鉆,提高了制孔質量和刀具耐用度。三尖鉆是在鉆頭外緣轉點處設計兩個凸出的尖刃口,專門用于纖維的割斷,防止出現毛刺以及孔口的撕裂。雖然三尖鉆可以有效地控制孔口的毛刺,但其主切削刃的強度也受到削弱。表1是目前碳纖維復合材料鉆削研究中主要應用的刀具類型。
民用飛機翼梁、桁條和蒙皮等結構件通常由各種不同成分的碳纖維復合材料構成。碳纖維復合材料結構件裝配時通常需要與作為承載支撐件(骨架或支架)的鈦合金和鋁合金零件局部連接,形成復合材料/合金(C/A,Composites/Alloy)疊層構件,C/A疊層構件主要采用鉚接和螺接的機械連接形式,裝配時需要加工大量連接孔。F-22戰斗機每副機翼上都有14000多個連接孔需要加工,一架波音747飛機則有300多萬個連接孔需要加工。CFRP和C/A疊層制孔成為飛機制造中極為重要的加工工序。
圖1 碳纖維復合材料制孔缺陷
連接孔的加工精度和質量是保證構件連接可靠性和壽命的關鍵。飛機碳纖維復合材料結構件制孔數量多、難度大、要求高、工作繁重,裝配制孔的精度和質量要求更高,對制孔技術提出了新的挑戰,亟需專用高性能制孔刀具和高效精密制孔工藝。
CFRP制孔的主要問題
飛機結構件碳纖維復合材料制孔存在的問題主要表現在以下幾個方面。
制孔精度和質量差,加工缺陷嚴重。如果采用傳統麻花鉆進行CFRP和C/A疊層制孔,鉆孔精度和表面質量差。特別是鉆孔時軸向切削力大,導致碳纖維復合材料產生纖維排列畸變、撕裂、層間分層和出口毛刺等缺陷,如圖1所示。鋁合金、鈦合金等由于屬于薄板制孔,也容易形成嚴重的出口毛刺。
制孔工藝流程長。由于缺乏合適的專用高性能刀具進行CFRP和C/A疊層制孔,為了保證C/A 疊層結構的制孔精度和質量,生產現場不得不采取“鉆孔-擴孔-粗鉸孔-精鉸孔-锪窩”多工序加工策略,造成工序和刀具多,成本高、工藝流程長、管理復雜,難以實現自動化。這是由于采用手持工具完成多工序加工時,制孔效率極低,制孔精度和質量的穩定性難以保證。
刀具磨損嚴重。由于碳纖維復合材料的硬度高和強度高等特點,導致刀具快速磨損,不僅影響加工精度和表面質量,而且使生產成本居高不下。
工藝參數匹配困難。C/A疊層制孔時,由于碳纖維復合材料與合金材料性質和可加工性差異很大,鉆削工藝參數的匹配和控制不當會導致嚴重的界面缺陷和出、入口缺陷。
制孔過程排屑不暢,熱影響嚴重。C/A 疊層結構制孔時,特別是CFRP/Ti合金疊層制孔時,鉆削合金會產生連續的高溫切屑,不僅不易排屑,而且高溫切屑排出時容易劃傷或燙傷復合材料內孔表面,影響制孔質量。
綜上所述,CFRP和C/A 疊層構件制孔與傳統金屬制孔具有巨大的區別,專用高性能制孔刀具和高效精密制孔工藝已成為航空航天領域復合材料構件裝配中的關鍵技術。
碳纖維復合材料制孔加工刀具性能要求
碳纖維復合材料制孔中應用的刀具結構類型較為復雜,主要包括麻花鉆(Twist drill)、匕首鉆(One shot drill reamer)、多面鉆(Multi-facet drill)、三尖鉆(Kevlar drill)、套料鉆(Core drill)等。通過鉆尖形貌和刀具角度的優化使得在鉆削碳纖維復合材料時碳纖維的切斷更輕快、順利,從而獲得更小的軸向力、更低的鉆削溫度、更高質量的孔是刀具匹配性能研究的主要目標。
在碳纖維復合材料加工中,大負前角的橫刃易引起過大的軸向力并可能造成分層。因此,通常采用X型或S型橫刃修磨方式來改變橫刃。匕首鉆嚴格來講是一種鉆、鉸復合刀具,由于有周向側刃作為主切削刃直接參與鉆孔,更易形成無毛刺、表面高質量的孔。匕首鉆在抑制毛刺生長方面的作用,在許多研究人員的試驗研究中得到了證實。多面鉆在碳纖維復合材料鉆削的應用,源于美國洛克希德公司通過成功采用八面鉆,提高了制孔質量和刀具耐用度。三尖鉆是在鉆頭外緣轉點處設計兩個凸出的尖刃口,專門用于纖維的割斷,防止出現毛刺以及孔口的撕裂。雖然三尖鉆可以有效地控制孔口的毛刺,但其主切削刃的強度也受到削弱。表1是目前碳纖維復合材料鉆削研究中主要應用的刀具類型。
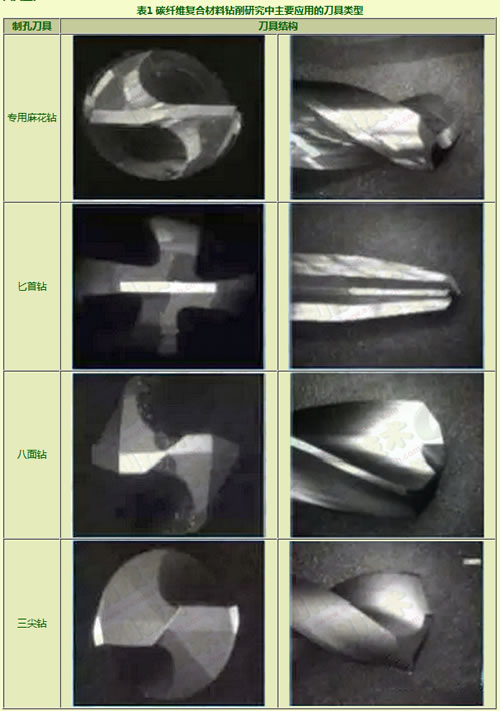
表1 碳纖維復合材料鉆削研究中主要應用的刀具類型制孔刀具刀具結構
碳纖維復合材料的加工過程中,刀具材料普遍采用PCD或金剛石涂層硬質合金。目前,金剛石涂層硬質合金刀具已成為解決碳纖維復合材料專用刀具磨損及刀具壽命短的關鍵技術。
碳纖維復合材料制孔刀具試驗研究
本次試驗所用材料為多向鋪層碳纖維復合材料層合板,每層均為單向單層,層合板鋪層共有32個鋪層。板材尺寸規格為300mm×200mm×6mm,如圖2所示。試驗刀具在結構形式方面涉及金剛石涂層硬質合金多面鉆、硬質合金匕首鉆,如圖3所示,刀具直徑6.35mm。試驗在DMG DMU70V數控加工中心上進行,采用KISTLER 9129AA壓電式測力儀、KISTLER5070電荷放大器組成的測量系統測量切削力和扭矩,采用KEYENCE VHX-600超景深顯微鏡檢測刀具磨損和觀測制孔形貌和毛刺情況。
碳纖維復合材料制孔刀具試驗研究
本次試驗所用材料為多向鋪層碳纖維復合材料層合板,每層均為單向單層,層合板鋪層共有32個鋪層。板材尺寸規格為300mm×200mm×6mm,如圖2所示。試驗刀具在結構形式方面涉及金剛石涂層硬質合金多面鉆、硬質合金匕首鉆,如圖3所示,刀具直徑6.35mm。試驗在DMG DMU70V數控加工中心上進行,采用KISTLER 9129AA壓電式測力儀、KISTLER5070電荷放大器組成的測量系統測量切削力和扭矩,采用KEYENCE VHX-600超景深顯微鏡檢測刀具磨損和觀測制孔形貌和毛刺情況。
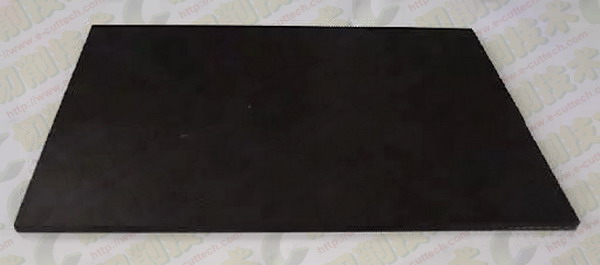
圖2 試驗用多向鋪層碳纖維復合材料層合板
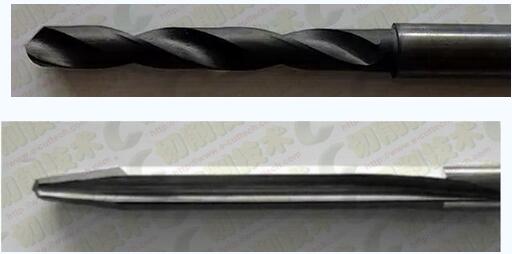
圖3 試驗刀具金剛石涂層硬質合金多面鉆
(上圖:與硬質合金匕首鉆;下圖:試驗結果分析)
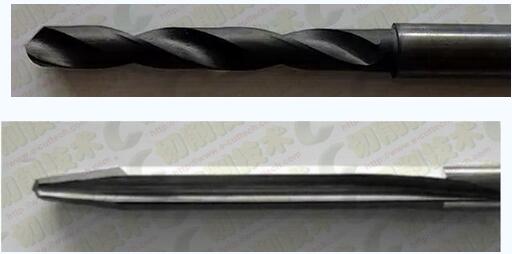
圖3 試驗刀具金剛石涂層硬質合金多面鉆
(上圖:與硬質合金匕首鉆;下圖:試驗結果分析)
(1)金剛石涂層硬質合金多面鉆
表2所示為金剛石涂層硬質合金多面鉆的制孔試驗結果。高轉速和低進給可以獲得較小的鉆削軸向力,有利于避免碳纖維復合材料加工分層和毛刺產生。因此,采用表中加工參數,轉速10000rpm、進給速度40mm/min,或者轉速8000rpm、進給速度80mm/min,可以獲得較小的軸向力。
表2所示為金剛石涂層硬質合金多面鉆的制孔試驗結果。高轉速和低進給可以獲得較小的鉆削軸向力,有利于避免碳纖維復合材料加工分層和毛刺產生。因此,采用表中加工參數,轉速10000rpm、進給速度40mm/min,或者轉速8000rpm、進給速度80mm/min,可以獲得較小的軸向力。
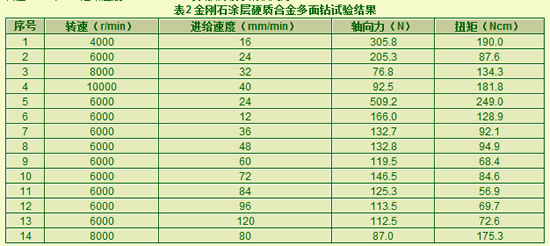
表2 金剛石涂層硬質合金多面鉆試驗
在上述參數下,制孔形貌如表3所示。兩種參數均獲得了良好的孔出口質量和入口質量,考慮制孔效率,優先選用轉速8000rpm、進給速度80mm/min作為金剛石涂層硬質合金多面鉆加工參數。
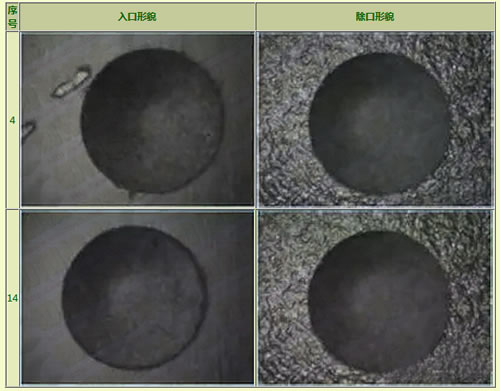
表3 金剛石涂層硬質合金多面鉆制孔形貌序號入口形貌除口形貌
(2)硬質合金匕首鉆
表4所示為硬質合金匕首鉆的制孔試驗結果。匕首鉆適用于低速小進給加工,高轉速會產生較高的加工溫度引起碳纖維復合材料燒傷。結合表5中的制孔形貌,采用表中加工參數,轉速4000rpm、進給速度16mm/min,作為優化加工參數。
表4所示為硬質合金匕首鉆的制孔試驗結果。匕首鉆適用于低速小進給加工,高轉速會產生較高的加工溫度引起碳纖維復合材料燒傷。結合表5中的制孔形貌,采用表中加工參數,轉速4000rpm、進給速度16mm/min,作為優化加工參數。

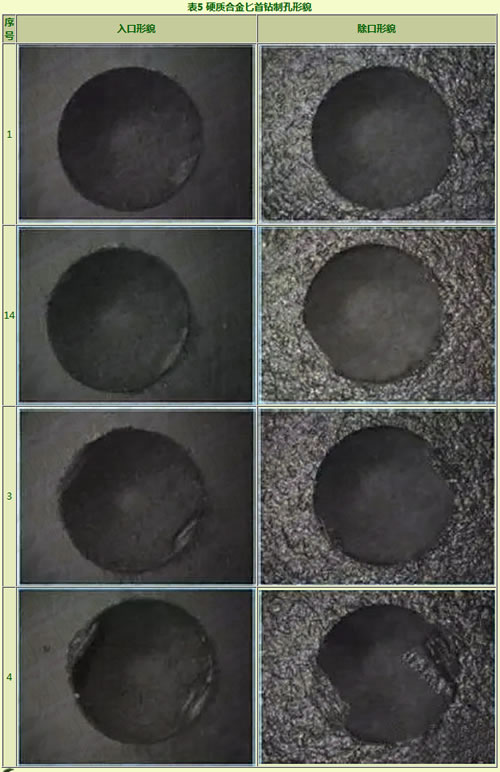