摘要 大余量、重負荷、自動化砂帶磨削典型案例:汽車發動機連桿端頭、鍋爐管線拋磨、核電高壓容器磨削等。磨削設備的特點:1.由于磨削余量大(1mm以上),磨削設備采取多工位,砂帶拋磨與砂輪磨...
大余量、重負荷、自動化砂帶磨削典型案例:汽車發動機連桿端頭、鍋爐管線拋磨、核電高壓容器磨削等。
磨削設備的特點:
1.由于磨削余量大(1mm以上),磨削設備采取多工位,砂帶拋磨與砂輪磨削相結合或者砂帶與砂輪互換的形式;
2. 工件體積龐大,相應的磨床的整體尺寸也很大,質量重;
3.磨削設備工作時間長,工作環境惡劣;
4.自動化拋光。
1.汽車發動機連桿端頭大余量減薄強力高效砂帶磨削
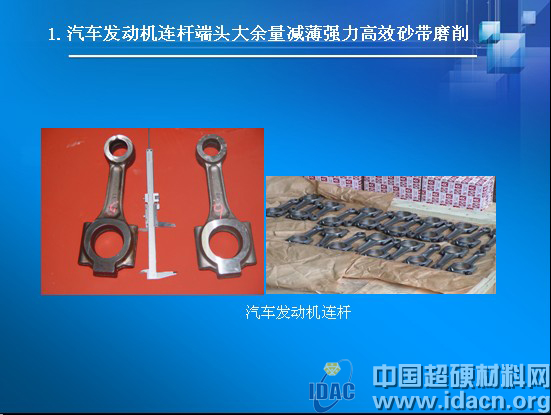
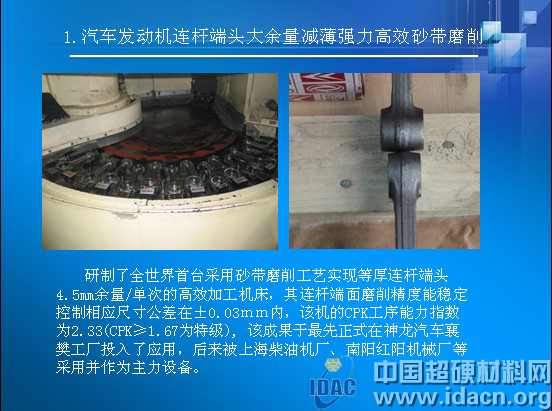
研制了全世界首臺采用砂帶磨削工藝實現等厚連桿端頭4.5mm余量/單次的高效加工機床,其連桿端面磨削精度能穩定控制相應尺寸公差在±0.03mm內,該機的CPK工序能力指數為2.33(CPK≥1.67為特級), 該成果于最先正式在神龍汽車襄樊工廠投入了應用,后來被上海柴油機廠、南陽紅陽機械廠等采用并作為主力設備。
2.鍋爐管線砂帶磨削
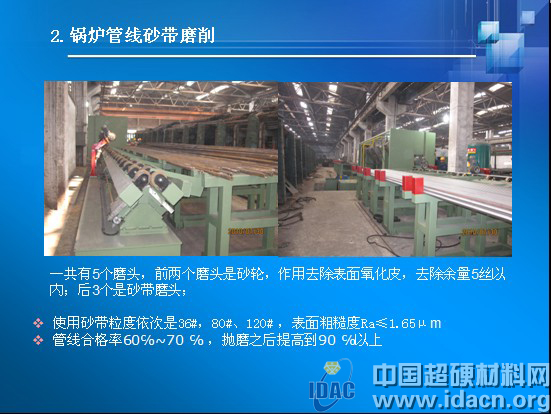
一共有5個磨頭,前兩個磨頭是砂輪,作用去除表面氧化皮,去除余量5絲以內;后3個是砂帶磨頭。使用砂帶粒度依次是36#,80#、120# ,表面粗糙度Ra≤1.65μm;管線合格率60℅~70 ℅ ,拋磨之后提高到90 ℅以上。
3.西氣東輸螺旋鋼管焊縫強力高效砂帶磨削
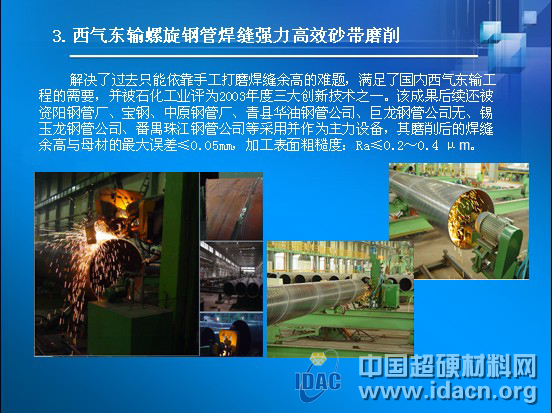
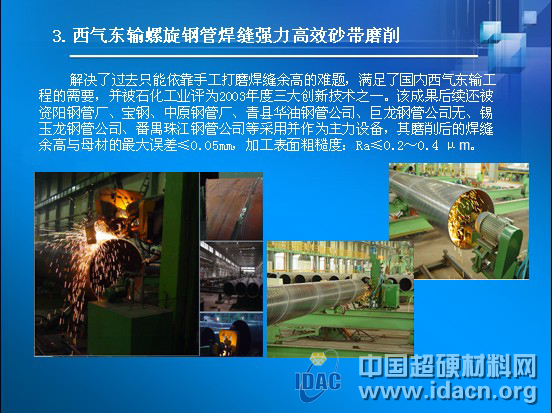
解決了過去只能依靠手工打磨焊縫余高的難題,滿足了國內西氣東輸工程的需要,并被石化工業評為2003年度三大創新技術之一。該成果后續還被資陽鋼管廠、寶鋼、中原鋼管廠、青縣華油鋼管公司、巨龍鋼管公司無、錫玉龍鋼管公司、番禺珠江鋼管公司等采用并作為主力設備,其磨削后的焊縫余高與母材的最大誤差≤0.05mm,加工表面粗糙度:Ra≤0.2~0.4 μm。
4.核電高壓容器焊縫坡口及堆焊層的高效精密砂帶磨削
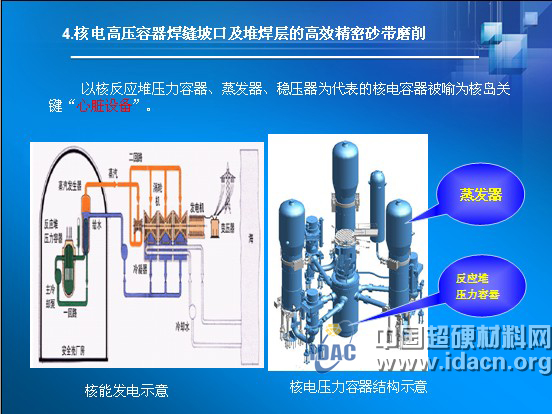
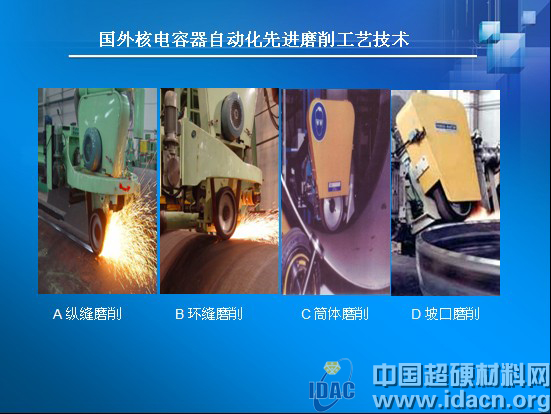
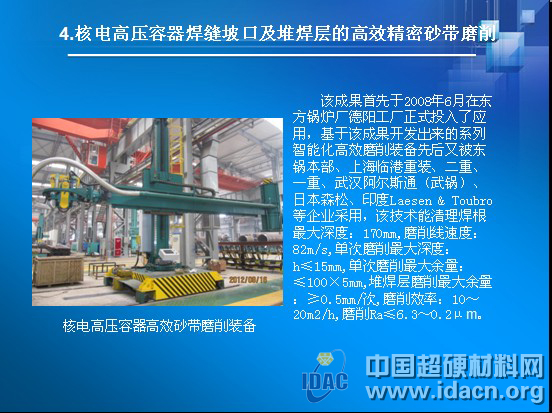
該成果首先于2008年6月在東方鍋爐廠德陽工廠正式投入了應用,基于該成果開發出來的系列智能化高效磨削裝備先后又被東鍋本部、上海臨港重裝、二重、一重、武漢阿爾斯通(武鍋)、日本森松、印度Laesen & Toubro等企業采用,該技術能清理焊根最大深度:170mm,磨削線速度:82m/s,單次磨削最大深度:h≤15mm,單次磨削最大余量:≤100×5mm,堆焊層磨削最大余量:≥0.5mm/次,磨削效率:10~20m2/h,磨削Ra≤6.3~0.2μm。

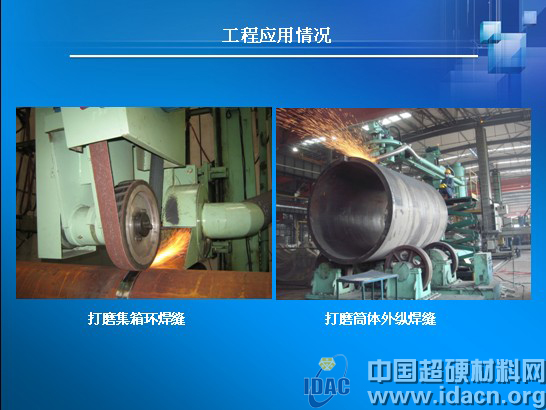
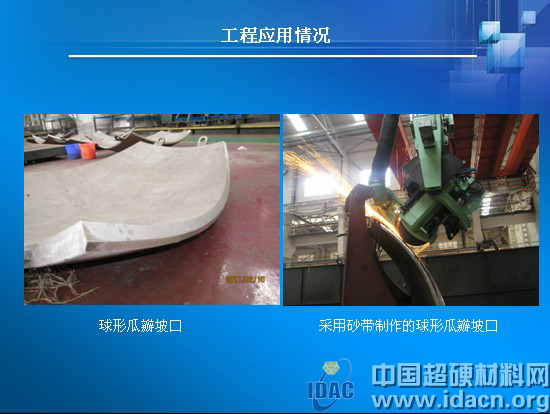
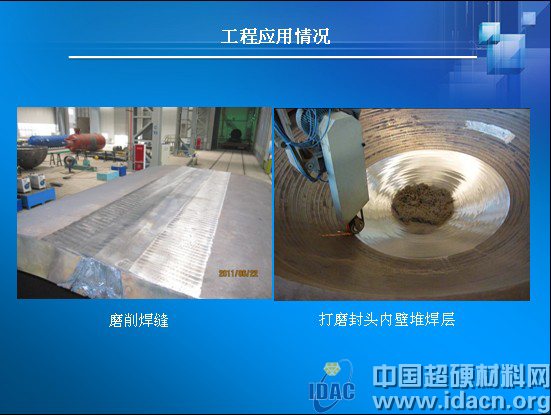