HPM75無磁鋼的加工分析
HPM75無磁鋼這種特殊材料因為它的合金成分中含有大量合金碳化物,這樣使得無磁鋼基體強化。但是我們切削機加工中所用到的普通鉆頭和刀具耐熱、耐磨性較差,硬度也相對來說較低。
刀具在對HPM75無磁鋼進行切削速度較低時,材料的切削底面和刀具的前刀面在切削過程中形成化學活性很高的材料新表面。材料表面在高溫、高壓的作用下,就會產生積屑流。積屑流在材料表面有相對的穩定性,但是當切削過程中振動或負荷不均勻時,積屑流則會脫落產生刀具磨損。超出刀刃的積屑流,將替代刀刃進行切削,這樣一來就會在已加工好了的材料表面留下痕跡,影響加工精度。
而HPM75無磁鋼模具件在鉆削過程中受至劇烈的加壓和沖擊壓力時,無磁鋼的奧氏體組織容易轉變為細晶粒的馬氏體,無磁鋼材料的硬度也就由原來的200HB(約20HRC)提高到550HB(約55HC)左右。在摩擦與擠壓形成的高溫下材料表面易形成高硬氧化層(Mn2O3),同時也使得材料導熱率很低(約為S45C模具鋼的25%),散發熱量少。這樣一來鉆頭易退火,產生切削刃口的壓潰,從而影響刀具壽命。
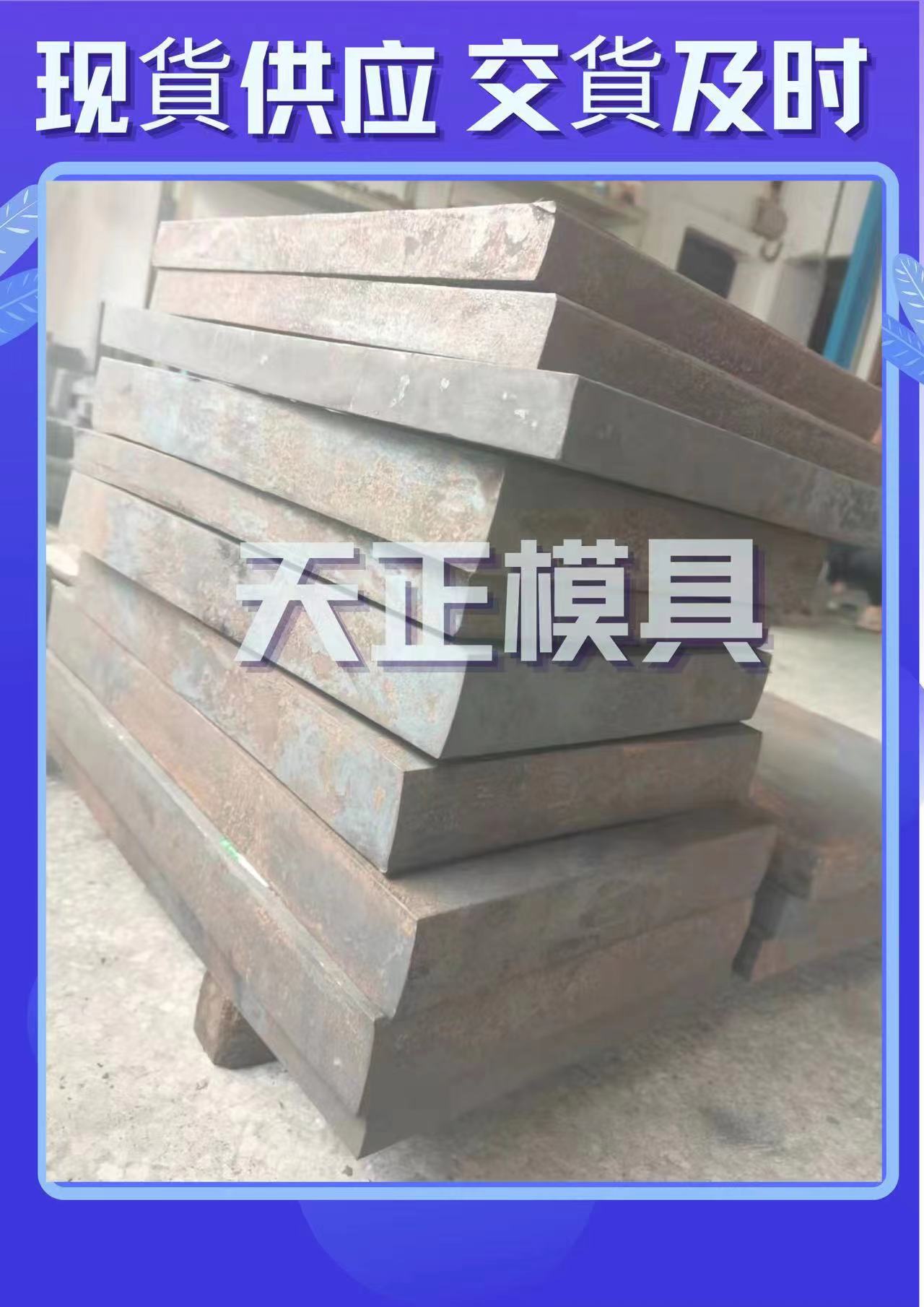
車削工藝
HPM75材料是高錳無磁鋼屬于高硬度、難切削的特殊鋼材,加工過程中高速切削過程中易產生崩碎切屑,這樣一來就會導致切屑力度就集中在刀刃旁邊的很小面積上,而局部壓力就很大,有一定的沖擊性。
所以HPM75無磁鋼的加工刀具應選抗彎強度和韌性較好的C-Co合金鋼刀。由于無磁鋼切削過程中很容易產生冷作硬化,所以選擇刀具前角大、后角小、刃弧半徑小的刀片,以此來降低切削力避免材料塑變嚴重。
鉆削工藝
HPM75無磁鋼鉆削加工中,鉆頭直徑的選擇主要是根據加工伯孔徑尺寸確定,根據產品實際需要通常為某一定值,而不參與優化。因此鉆削工藝優化主要從影響刀具耐用因素考慮,即鉆頭材料、角度、進給量及冷卻方式等。